Research and Development
Continuous Spray Freeze-Drying Technology
Designed for Injectable Solutions
MORIMOTO-LYO TM
Designed for Injectable Solutions
Our vacuum freeze-drying equipment and vacuum drying method are protected by Japanese patent JP6777350B1 and US patent 11,175,093.
Morimoto’s Aseptic Continuous Spray Freeze Drying Technology
Aseptic freeze-drying is traditionally performed by filling vials with a liquid solution and then drying using a shelf freeze dryer in batches. While shelf freeze-drying is well established and has a long history of use inside the pharmaceutical industry, it has slow sublimation and drying rates, making it both time-consuming and energy-intensive. A single batch can take several days or even up to two weeks to process. Additionally, based on the exact contour of each vial and position, the heating profile and drying experienced are different. For example, vials near the wall or door will be at different actual temperatures than vials in the center (called the edge vial effect). Naturally, this causes unavoidable within-batch variability and results in a non-uniform batch of vials, a well-known flaw with shelf freeze dryers. Differences between vials can lead to the entire batch being rejected due to aesthetic defects, loss of drug potency, or moisture levels that are out of specification.
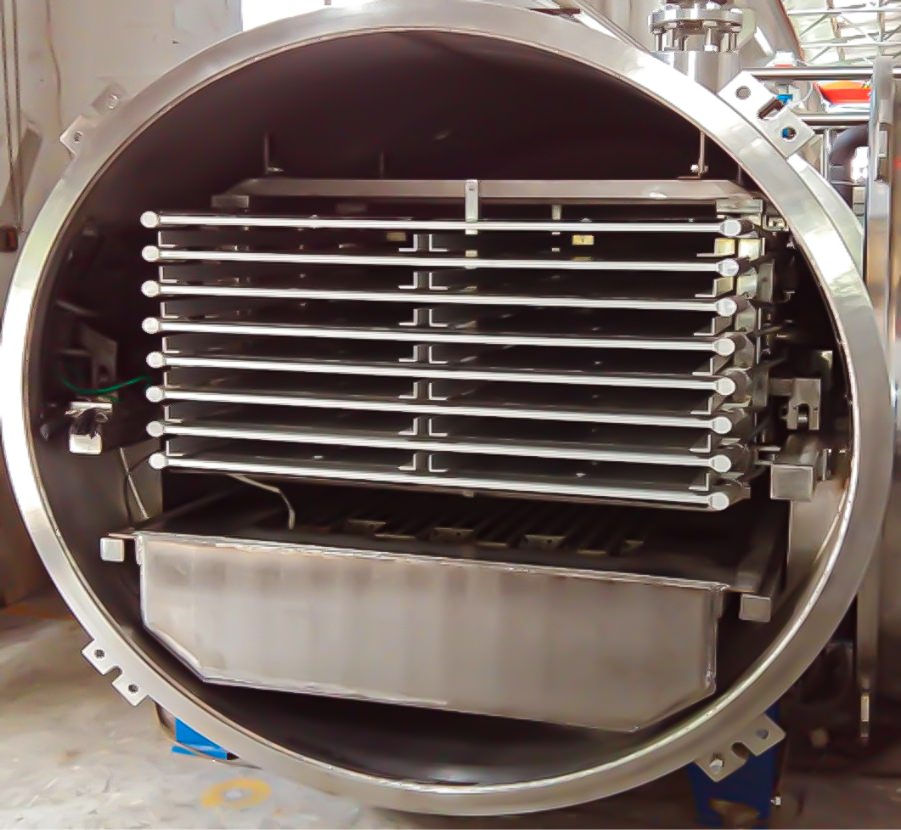
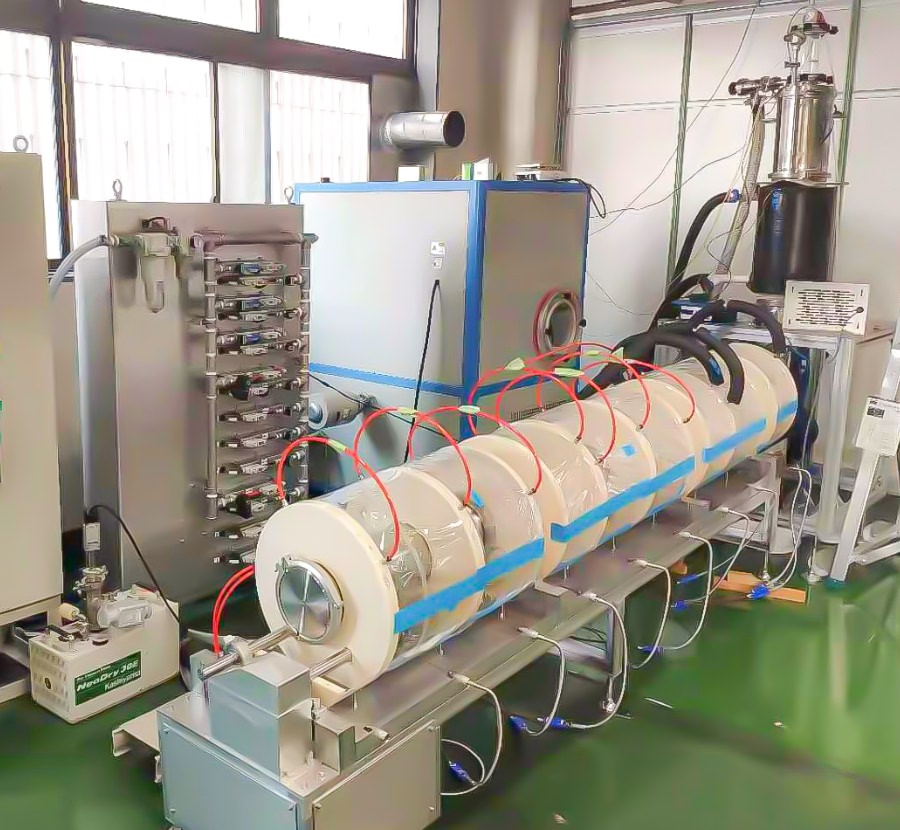
The new LYO by Morimoto-Pharma utilizes the latest technology and offers a continuous aseptic process for spray freeze-drying with superb performance.
A liquid feed solution is continuously sprayed into a cryogenically cooled vacuum freezing tower. The solution freezes into a frozen powder as it falls and is then transferred to the attached vacuum rotary dryer. Inside the rotary dryer, the frozen powder is heated through contact with the metal walls and is in constant motion as it moves forward. This allows for precise temperature control, rapid sublimation, and also prevents aggregation.
Long used in the food industry, continuous freeze-drying has seen limited use in the pharmaceutical industry due to not being able to meet the strict requirements. The MORIMOTO-LYO was designed from the ground up with pharmaceuticals and specifically injectable solutions, in mind. Morimoto plans to be a worldwide leader in making the use of continuous technology for pharmaceutical lyophilization widespread.
Comparison of Morimoto Technology
and Shelf-Style Lyophilization
High Productivity, Stability, and Uniformity
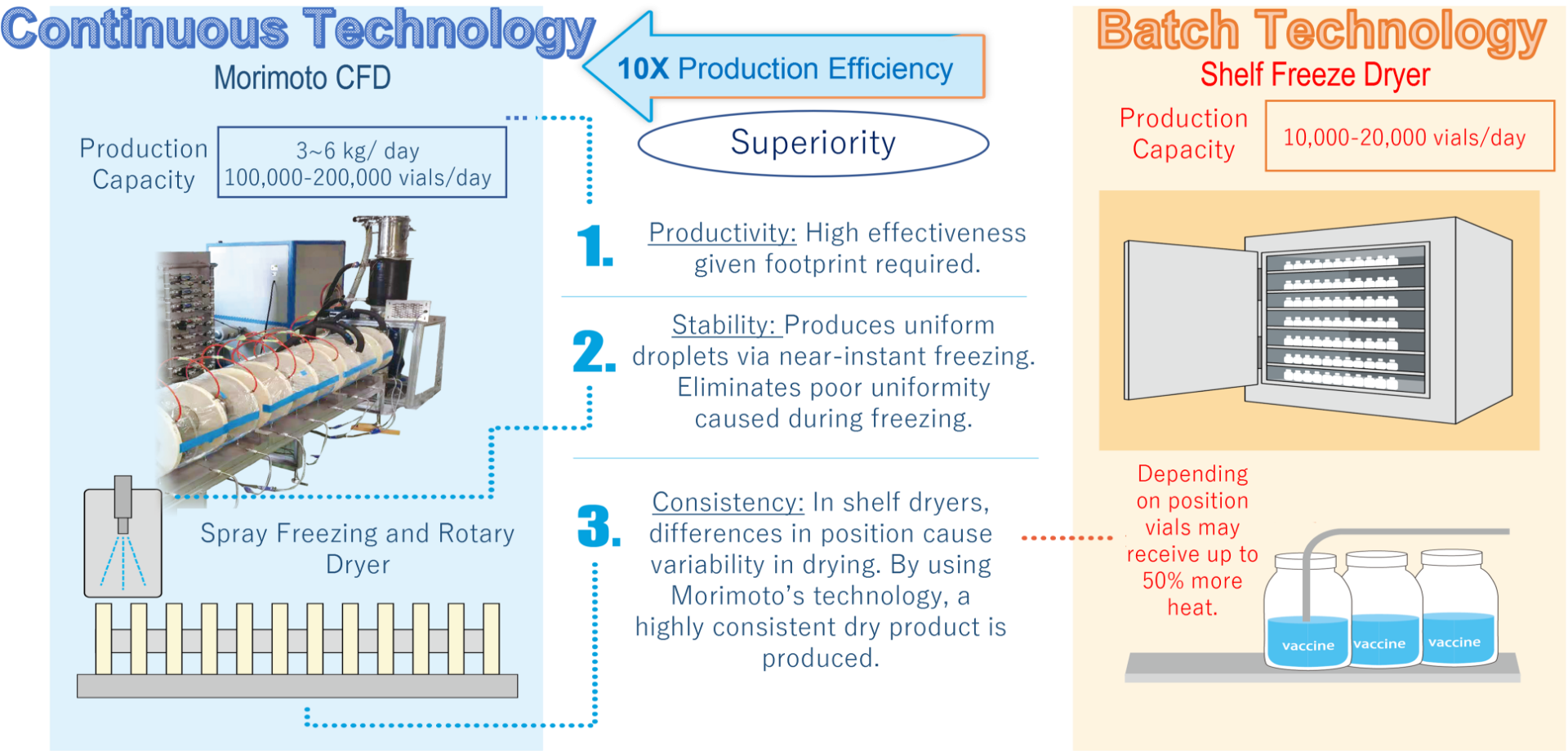
The Spraying Process
A liquid feed is sprayed into the vacuum freezing tower via special nozzles. As the droplets evaporate they disperse, drop in temperature, and then freeze. The nozzles were designed to provide dense particles with high flowability. Parameters such as nozzle size, flow rate, and nozzle temperature all affect the size of the initial droplets. A wide variety of nozzle sizes are available and temperatures are controlled to produce an optimal spray that rapidly freezes.
Unlike other spray technologies, the MORIMOTO-LYO uses vacuum freezing to freeze the feed solution
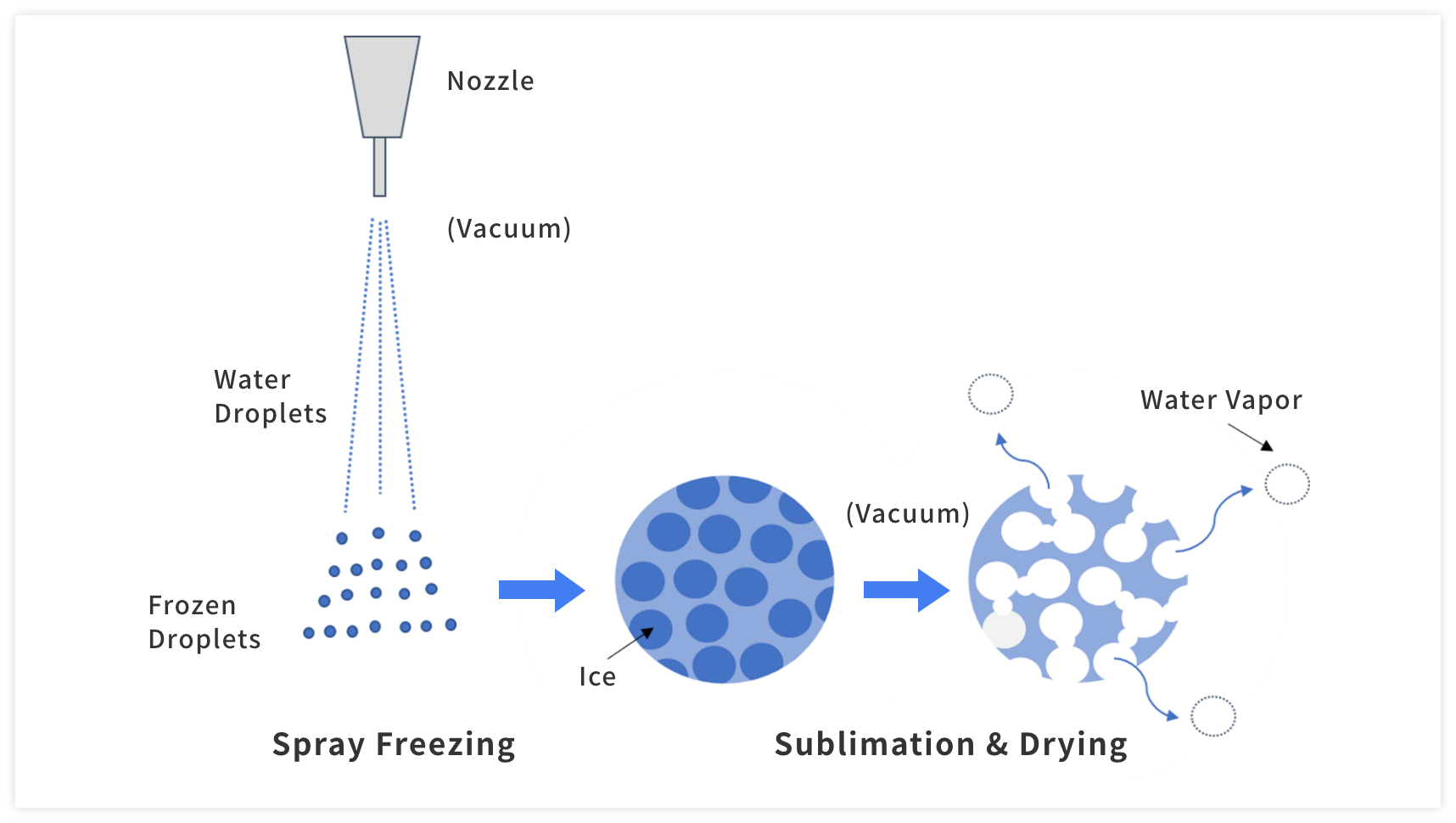
The Freezing Process
After being sprayed into the vacuum freezing tower, the water droplets continuously evaporate. Because evaporation is endothermic, the droplets drop in temperature and become smaller as they evaporate until they freeze. This process occurs in the order of seconds.
The initial temperature, droplet size, and pressure settings heavily influence the time required for freezing. With simple formulations, freezing is more rapid, while more complex formulations may require longer to freeze.
The properties of the initial frozen powder have a strong influence on the physical properties of the final dried powder. Thus, adjusting parameters during freezing to produce an ideal frozen powder is desirable to obtain the best possible final product.
The Drying Process
After freezing, the frozen powder is transferred into the attached vacuum rotary drying cylinder. As the cylinder rotates, the powder is moved forward through temperature-controlled zones and slowly heated to provide the necessary energy for sublimation and drying.
Unlike traditional bulk rotary drying, there is a very high contact with the metal surface and rapid temperature equilibration. Each section is monitored by sensors and the temperature is tightly controlled. This ensures consistent drying. Vacuum conditions are maintained to prevent melting and also to facilitate sublimation and drying.
In traditional batch freeze-drying, a single ice condenser is used to condense water vapor after sublimation. Between batches, it is defrosted and drained. The MORIMOTO-LYO features double ice condensers that are cycled and dried in turn, allowing for continuous operation.
During freezing, water freezes not only on the surface but throughout the particles. This ice is removed via sublimation during the drying process, leaving deep cavities. The result is a final powder that is extremely porous, and due to this high porosity, dissolution of the freeze-dried product is nearly instantaneous.
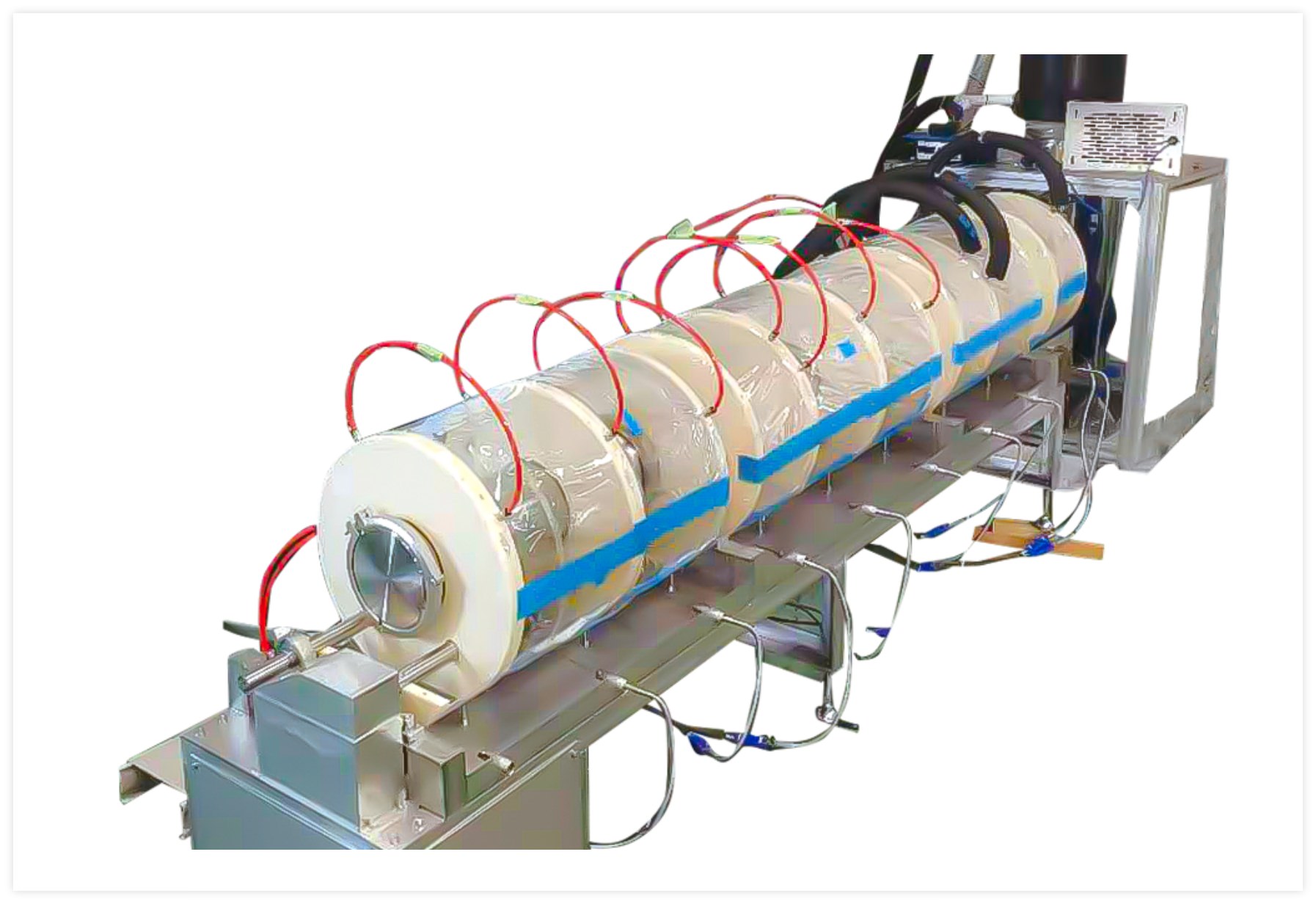